Blog
Demystifying the Weld Stud Selection Process: Material, Size, and Application Considerations
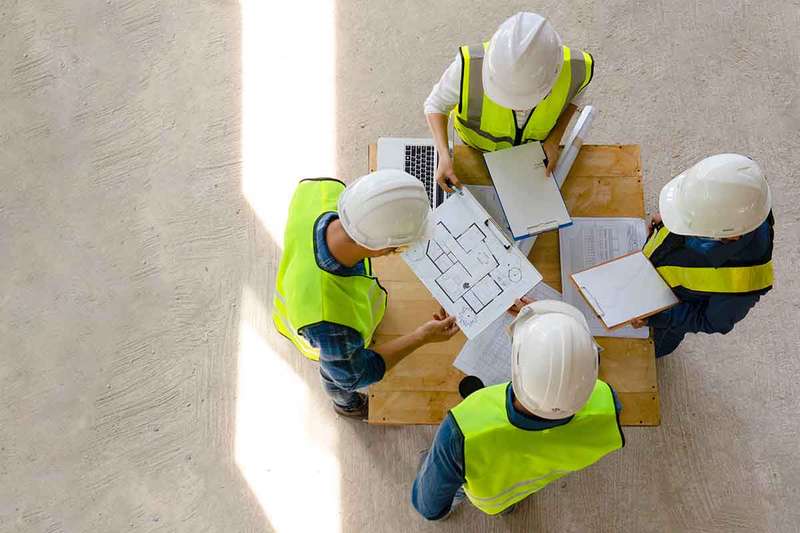
Understanding weld stud selection is essential for any industry reliant on secure, reliable fastening. The nuances of material, size, and application all play a part in choosing the right stud to deliver strength, safety, and longevity. This guide aims to give you the knowledge to master the selection process.
Mastering the Art of Weld Stud Selection
In the process of stud welding, selecting the right stud is paramount. It's a nuanced practice that involves understanding the potential of weld studs in different applications, their impact on performance and durability, and how they contribute to cost efficiency.
Unlocking the Potential of Weld Studs in Industrial Applications
Weld studs are an essential component across a range of industrial applications. Their potential extends far beyond mere fastening—they are a critical part of manufacturing processes in industries as varied as automotive, shipbuilding, construction and others. The strength, reliability, and versatility of weld studs can provide innovative solutions to various challenges in these industries.
Boosting Performance and Durability with the Right Choice
Opting for the correct weld stud directly enhances the performance and durability of your end product. A well-chosen stud boosts the overall performance of an assembly, reducing maintenance needs, improving conductivity, and allowing for innovative assembly designs. Durability, on the other hand, is enhanced by selecting a stud resistant to wear and tear, thus extending the product lifespan.
Cutting Costs and Maximizing Efficiency Through Proper Selection
Selecting the appropriate weld stud not only boosts performance and durability but also cuts costs and enhances efficiency. Proper selection means fewer replacements, less maintenance, and a streamlined assembly process. All these benefits combined lead to cost savings and increased productivity, underscoring the importance of careful, thoughtful selection.
Navigating the Material World of Weld Studs
When it comes to weld studs, one size does not fit all. Different materials bring unique advantages and considerations to the table. Deciding on the right material for your weld stud can be complex, but understanding the advantages and trade-offs of each option can simplify this process.
Exploring Mild Steel, Stainless Steel, and Aluminum Stud Options
The material of your stud is a paramount factor in selection. Common materials include mild steel, stainless steel, and aluminum. Mild steel is a versatile and economical choice, but it requires protective measures against corrosion. Stainless steel offers exceptional corrosion and heat resistance, albeit at a higher cost. Aluminum, on the other hand, combines lightweight and strength with excellent corrosion resistance, but it relatively difficult to weld.
Balancing Corrosion Resistance and Material Compatibility
It's not just about picking a material with excellent properties—you also need to consider the compatibility of the stud material with the parent material. An incompatible match may result in a weaker joint, ultimately compromising the integrity of the application. Hence, corrosion resistance and material compatibility must be balanced to select the optimal weld stud.
Aligning Material Selection with Welding Process Requirements
The welding process also influences material selection. Different processes have distinct requirements and work differently with various materials. Knowing the process you'll be using can guide your selection to ensure a successful weld.
Size Matters: Optimal Configuration for Weld Studs
Size and configuration are as crucial as the material when it comes to weld studs. The dimensions of a stud can influence its load-bearing capabilities, while the design can determine its suitability for particular applications.
The Ins and Outs of Diameter, Length, and Thread Pitch
Each aspect of a stud's size - its diameter, length, and thread pitch - contributes to its performance. The diameter of a stud typically corresponds to its strength, while its length should match the thickness and type of the parent material. For threaded studs, the thread pitch can affect the ease of installation and the stud's load-bearing capacity.
Weighing the Pros and Cons of Flanged vs. Non-Flanged Studs
The choice between flanged and non-flanged studs depends largely on the application. Flanged studs ensure additional contact for the weld, making them ideal for uneven or curved surfaces, whereas non-flanged studs are best suited to flat surfaces where achieving a good contact area is straightforward and reduced weld strength is acceptable.
Deciphering Load Capacities and Tensile Strength for Success
A stud's mechanical properties, including its load capacity and tensile strength, play a vital role in its selection. These characteristics indicate the robustness and durability of the stud, with higher values indicating stronger performance.
Tailoring Weld Stud Selection to Your Unique Applications
No two applications are the same, and thus, no two weld studs are identical. Your stud selection should match the specific requirements of your application, considering factors such as industry standards, environmental conditions, and the need for customization.
Meeting Industry Requirements and Standards Head-On
Every industry has its own set of standards for safety and performance, and the studs you select must meet these. For example, the studs required for automotive applications may differ from those needed for shipbuilding due to the differing conditions in these industries.
Adapting to Environmental and Operating Conditions
The conditions in which the assembly will operate should also inform your selection of a stud. For example, studs used outdoors in a marine environment will require high corrosion resistance, while those used in high-temperature settings may need to withstand heat.
Embracing Customization and Specialized Solutions
In some cases, unique applications may necessitate specialized weld studs. Custom weld studs offer unique material choices, sizes, or configurations to fit the specific needs of your project. By embracing customization, you can ensure that your weld studs meet the precise demands of your unique applications, enhancing the overall functionality and efficiency of your assembly.
Tapping into Industry Knowledge for Ideal Weld Stud Selection
Choosing the right weld stud is an art that relies heavily on experience and in-depth knowledge. It requires a comprehensive understanding of the industry's workings, including the latest technological advances, evolving industry standards, and emerging trends. Leveraging industry knowledge can help you make optimal weld stud selections that align with your objectives and improve your project's overall outcome.
As a leader in the world of stud welding, Image Industries offers a wealth of knowledge and expertise to help guide your weld stud selection process. With a comprehensive understanding of material choices, size considerations, and the diverse applications of weld studs, we are well-equipped to help you navigate the complex landscape of weld stud selection. Together, we can ensure that your projects reach new heights of success.
Selecting the right weld stud can be a game-changer for your projects. By considering factors such as material, size, and application, you can make informed choices that enhance the performance, durability, and cost-effectiveness of your assemblies. While the task may seem daunting, with the right knowledge and guidance, you can demystify the process and transform it into an opportunity to excel in your industry. Contact Image Industries for help choosing the right weld studs today or give us a call at (847) 793-1943.
Building lasting bonds since 1976.
Providing superior stud welding and stud welder parts and equipment isn't enough. We also strive to deliver better service and unmatched expertise. And that's exactly what we've been doing for more than 40 years.
Read About Our History