Blog
Optimizing Performance: A Guide to Stud Weld Fastening Process
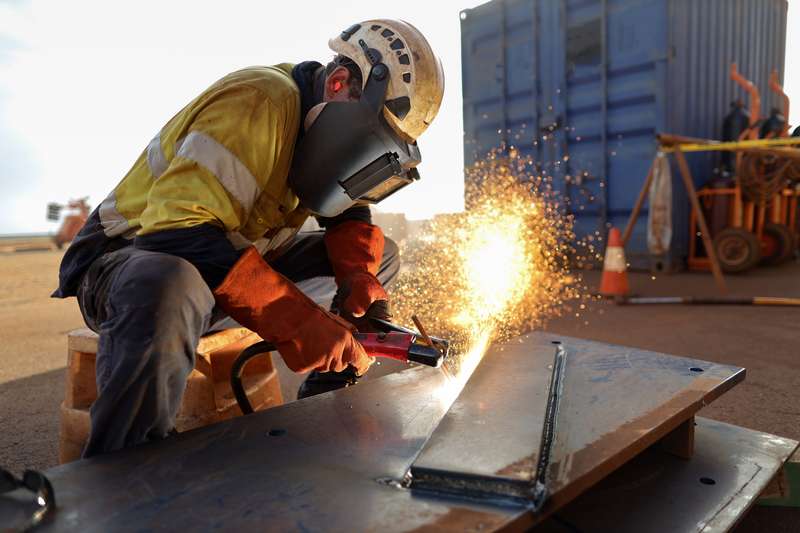
The Stud Welding Process
Stud welding is a reliable fastening method by which a metal fastener is welded to another metal part using an electric arc. It stands out for its speed, reliability, and strength of the resultant joint, making it a preferred method among professionals. This is an essential technique across a spectrum of sectors, including the engineering, construction, and manufacturing industries.
In stud welding, a variety of metals are commonly used, including stainless steel, mild steel, aluminum, and brass. The studs, which can be threaded, unthreaded, or internally threaded, range in diameter from 1/10” to 1” (3 mm to 25 mm). The selection of the right stud is critical to the success of the resulting weld.
Versatility of Stud Welding Applications
The versatility of stud welding is evident in its widespread use across various industries that depend upon consistent and durable joints.
Applications range from attaching small components such as switches and buttons to larger structural elements in shipbuilding, where maximum strength and structural integrity are crucial. Stud welding also finds its place in decorative and consumer items, offering both aesthetic appeal and functional strength.
The Advantages of Stud Welding
When compared to other fastening methods, stud welding offers several benefits. Its efficiency comes from requiring fewer steps and only one-sided access to the parent material.
This method results in strong joints without reverse marking, often stronger than the parent material or the stud itself. It eliminates issues associated with other methods, including leaking or staining from punching and deburring holes.
Stud Welding Processes
Capacitor Discharge Stud Welding
Ideal for thin gauge metals, the capacitor discharge or CD method involves a stud with a pip being placed on a clean, flat metal sheet. A high current pulse from charged capacitors creates an arc, melting the pip and allowing the stud to forge to the sheet.
This method is suitable for materials ranging from .020” (0.5mm) thick and up, is fast and cost-effective, and suitable for curved or imperfect surfaces.
Drawn Arc Stud Welding
Drawn arc stud welding requires materials above 2mm. It accommodates larger diameter fasteners and is more flexible, making it an excellent option when working with curved or imperfect surfaces.
This method requires a 415-volt, three-phase power source and uses ferrules to contain the molten metal, ultimately adding extra steps to the procedure. Drawn arc stud welding is typically ideal for stud welding large diameters as well as multi-gun applications.
Short Cycle Stud Welding
Similar to drawn arc stud welding but without the need for ferrules or flux, short cycle stud welding uses inert shielding gas. This method is faster and suitable for high-volume applications but may produce weaker welds if not properly applied.
Short cycle stud welding is a delicate balance between speed and strength, and is more suitable for thicker materials than CD stud welding and also in accommodating imperfections in the metal sheets.
The Fundamentals of Stud Welding
To excel in stud welding, starting with a solid understanding of the basics is essential, which begins with ensuring material compatibility between the stud and base metal.
Using high-quality studs with consistent manufacturing standards is vital, as variations can lead to inconsistent welds. Regular equipment calibration is also necessary, as consistent energy output is critical for uniform welds.
Pre-Weld Preparation
The preparation phase is critical for achieving precision in stud welding. Surface cleanliness cannot be overstated here; any presence of dirt, oil, or rust can significantly impede the welding process and weaken the weld.
Proper alignment of the stud with the base metal is equally important, as misalignment can compromise the weld's integrity. Additionally, adjusting the welding machine to the appropriate settings for the specific type of metal and stud size being used is essential for optimal results.
Don’t forget, safety is absolutely vital when it comes to stud welding. Therefore, using appropriate personal protective equipment or PPE, regularly inspecting your equipment for possible damage, and maintaining a clean and organized workspace are all essential practices to minimize the risk of accidents and ensure a safe working environment.
The Welding Process
The actual process of stud welding requires controlled initiation, steady application, and optimal timing. Remember: a smooth start is essential for ensuring a clean, strong weld.
Maintaining a steady hand and even pressure throughout the welding process is essential to avoid fluctuations that can lead to uneven welds. Adhering to the correct weld time is also important; too short a time can result in a weak weld, while too long can damage the materials involved.
Professionals must be adept at adjusting their approach to accommodate variances, including adapting to material thickness variations, understanding the impact of temperature changes on the welding process, and adjusting settings for different stud sizes.
Learn more about the welding process here.
Post-Weld Inspection
After welding, each weld should be visually inspected for consistency and potential defects such as cracks or misalignment. Conducting strength tests on random welds ensures they meet the required standards for the project at hand.
Because of this, keeping detailed records of these quality checks can be invaluable for future referencing and maintaining consistent quality control.
The Industry’s Best Stud Weld Fastening Systems
Our comprehensive guide on stud welding fastening systems offers a pathway to mastering a technique foundational for all kinds of industrial applications.
With training, employees with or without a welding certification can achieve consistent, precise welds by adhering to the principles and practices outlined above, which are essential for the integrity and strength of the welds in their projects. From understanding the fundamentals to implementing safety-first protocols, each step contributes significantly to the quality of the welding outcome.
For those looking to further enhance their stud welding capabilities, Image Industries Inc. stands as an invaluable resource. Their extensive range of high-quality weld studs, advanced stud welding fastening systems, general stud welding equipment, and a wide array of stud welding accessories are here to help meet the diverse stud welding needs of businesses in all kinds of industries. Contact Image Industries today to learn more!
Building lasting bonds since 1976.
Providing superior stud welding and stud welder parts and equipment isn't enough. We also strive to deliver better service and unmatched expertise. And that's exactly what we've been doing for more than 40 years.
Read About Our History